
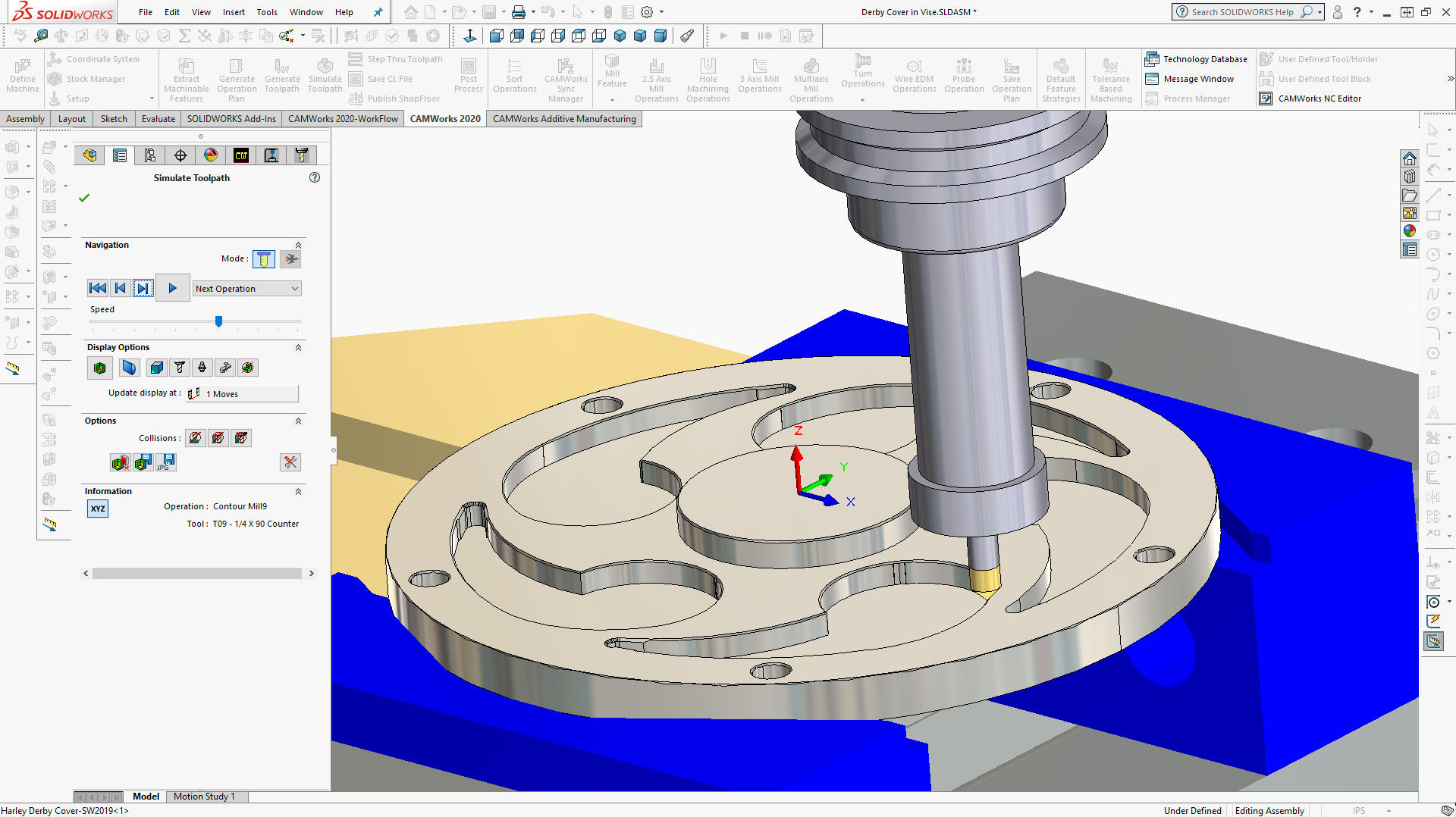
For example, bottom finishing, which requires minor tuning and tweaking, can largely be automated. Afterward, you might consider automating the operations your most common tools are used in. When considering which processes to automate, the standard feeds and speeds applied to your tools are generally a sound starting point.

As a result, you can scale repetitive processes through automation without increasing the risk of human error. In turn, you can focus on any unique part features that are not within your TechDB. CAMWorks TechDB remembers the specific processes and strategies you use in your manufacturing process and applies them via AFR. Large-scale operations without a strategic plan to mitigate human error, however, are likely to repeat the mistakes of the past. Small volume, high turn operations such as DEVELOP LLC are intimately familiar with the challenges posed by human error, implementing fail-safes to reduce the likelihood of accidents and costly mistakes as much as possible.Įven on a small scale, DEVELOP strategically maps out and combats human error. Fortunately, systematic processes can be implemented to reduce the chances of human error. Īll throughout the manufacturing process, human error has the potential to degrade quality, consistency, and safety. The following blog post will focus on leveraging CAM automation for the purposes of reducing human error, clearly defining a strategy, and ultimately, scaling. Overall, it’s important for teams to identify which aspects of their production cycle can be automated to yield the highest ROI.
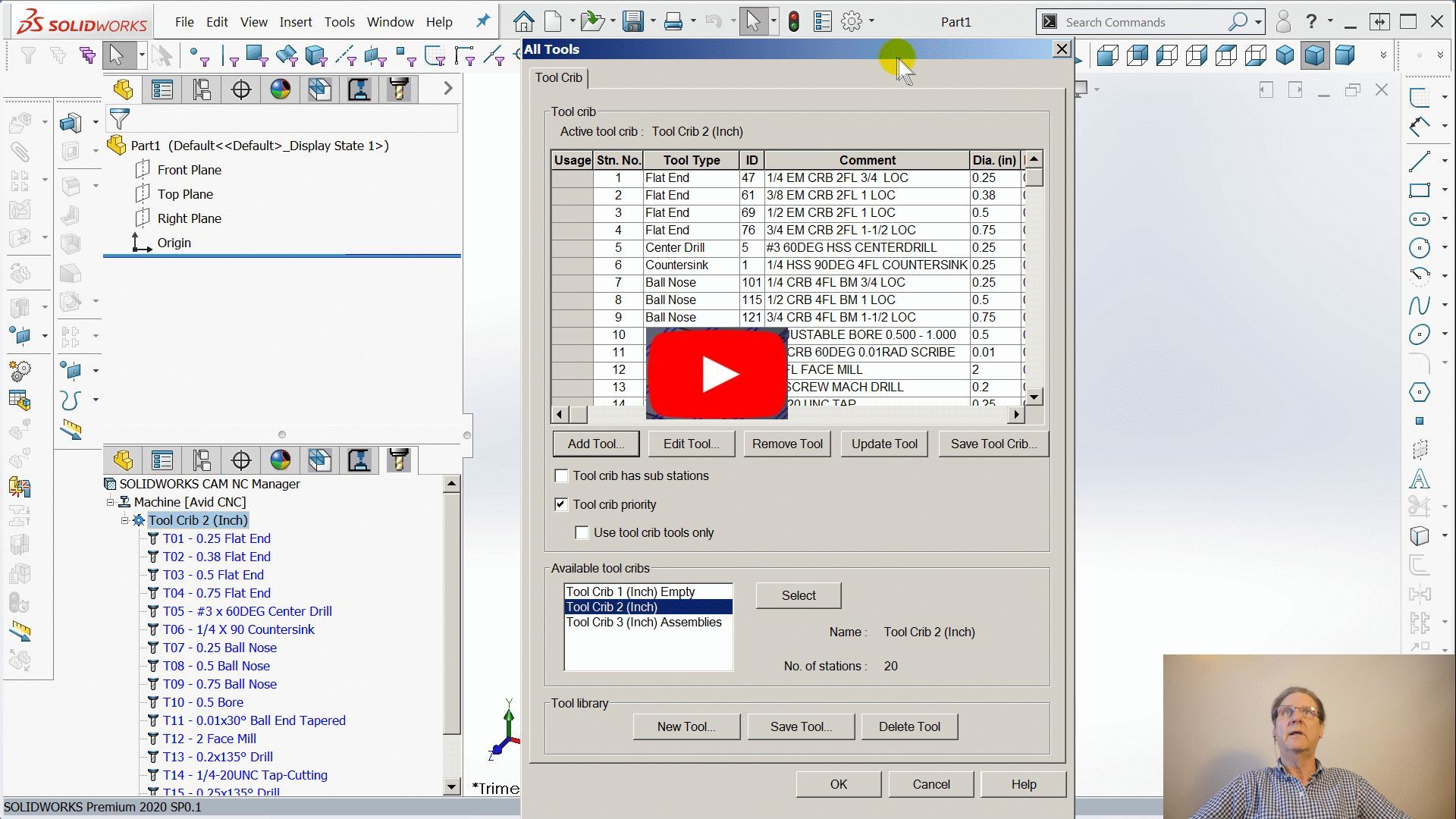
Although decision-makers in the manufacturing space are eager to automate 360° of their processes, incremental automations are key to making progress. When compared to lights out machining, these two facets offer comparable value or greater. For startups and small businesses alike, CAMWorks offers a myriad of benefits, specifically in reference to the Technology Database (TechDB) and Automated Feature Recognition (AFR).
